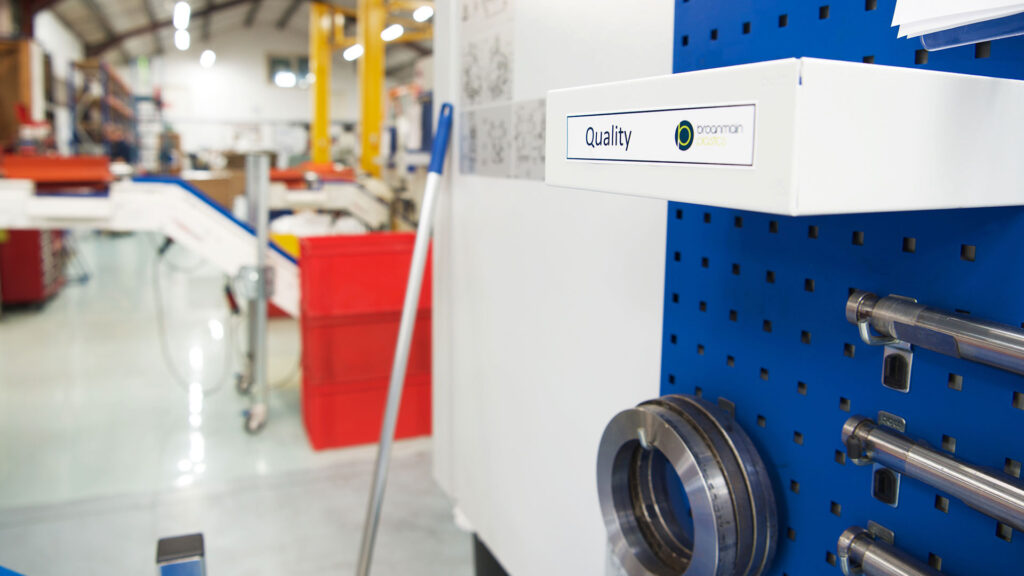
Quality is among the most important reshoring considerations say our customers
Trade wars, closed borders, shipment delays, ongoing tariff negotiations, currency fluctuations and Brexit are just a number of factors prompting UK manufacturers to assess their supply chain vulnerabilities. Many Broanmain customers have done it. Managing Director Jo Davis shares some lessons learned and why flexibility, quality control and fast turnaround are more important than cost alone.
Across the manufacturing world, protectionism has become the word of the moment. While the fallout from the crisis is both amplifying familiar manufacturing risks and creating new ones, the reshoring equation is complex. For those assessing their shoring business case and considering switching suppliers to a domestic technical moulder, cost considerations can not be purely about price per part, but the total benefit.
Among many things, value includes labour, locally sourced raw materials, minimum orders, shipment and tariffs, as well as part quality and reject volumes. Jo estimates that Broanmain customers who recently made the decision to reshore production to the UK weighed the benefits up against over 30 criteria.
Compared to the 1990s exodus to Asia it is clearly evident that manufacturers today are no longer led on price and labour costs alone. Jo explains: “ Having the capacity and skills to manufacture on domestic soil, having the space to hold inventory and meet short supply lead times, and quantifying the disruption risks and hidden costs that can accompany managing relationships and quality issues with a supplier located the other side of the world in a different time zone, are all equally important considerations.”
Assuming that COVID is the instigator of this reshoring drive is also short-sighted claims Jo, highlighting that British companies of all shapes and sizes were assessing their supply chain risks long before the pandemic struck. “Media coverage and medical equipment shortages simply heightened awareness of the vulnerabilities. However, proximity to a component supplier does help equipment manufacturers to monitor and resolve quality and precision challenges more directly, especially when lead times are short. It can also help to resolve red tape import challenges.
“The fact that COVID highlighted the low quantity of manufacturers in the UK has helped us raise our heads about this problem – but it has also allowed us to showcase our ingenuity and flexibility.”
Any move by manufacturers requires a good deal of forward planning and assessment of the long-term viability, cautions Jo. For some manufacturers, achieving the optimum mix of manufacturing efficiency and productivity might require a mix of offshoring, reshoring, nearshoring and backshoring.
“Applying our experience supporting a number of customers to bring technical moulding projects closer to home, we would always advise focusing on where you can expand production capacity in the UK initially. In time you might gradually move the entire supply chain. Inevitably, taking a more considered approach builds confidence and ensures that quality is not compromised during the transition,” adds Jo.
A poll early on in the pandemic indicated that 40% believed the UK would have a stronger domestic supply chain after COVID-19. Just over a quarter (26%) agreed that there would be increased adoption of automation and digital tools[1]. Jo concurs that the virus has been a catalyst to instigate a stronger focus on what Britain and Broanmain does best – technical engineering.
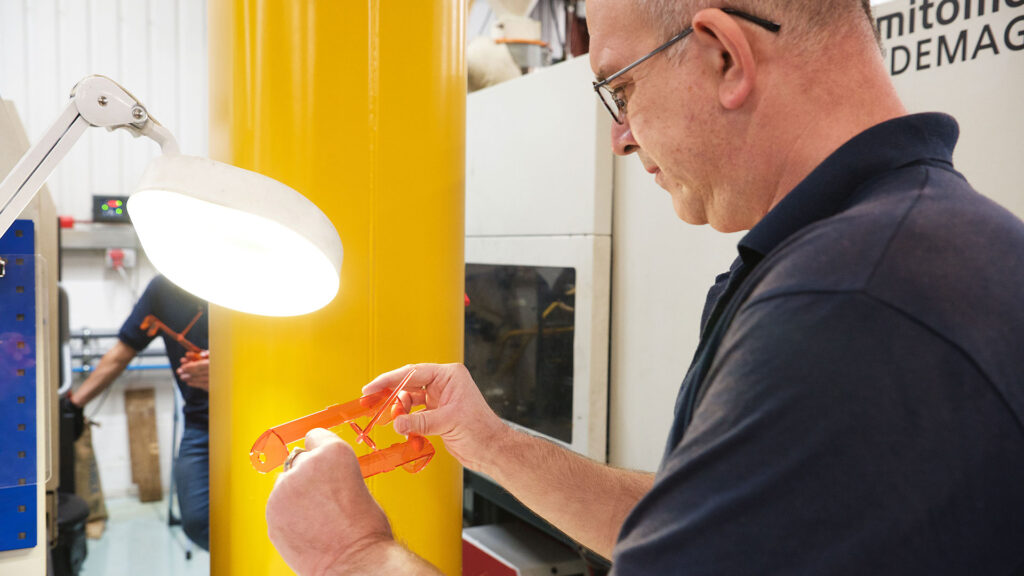
Technical and engineering prowess and equipment investment strengthens the rationale to reshore
[1] https://www.theengineer.co.uk/poll-covid19-engineering-impact/