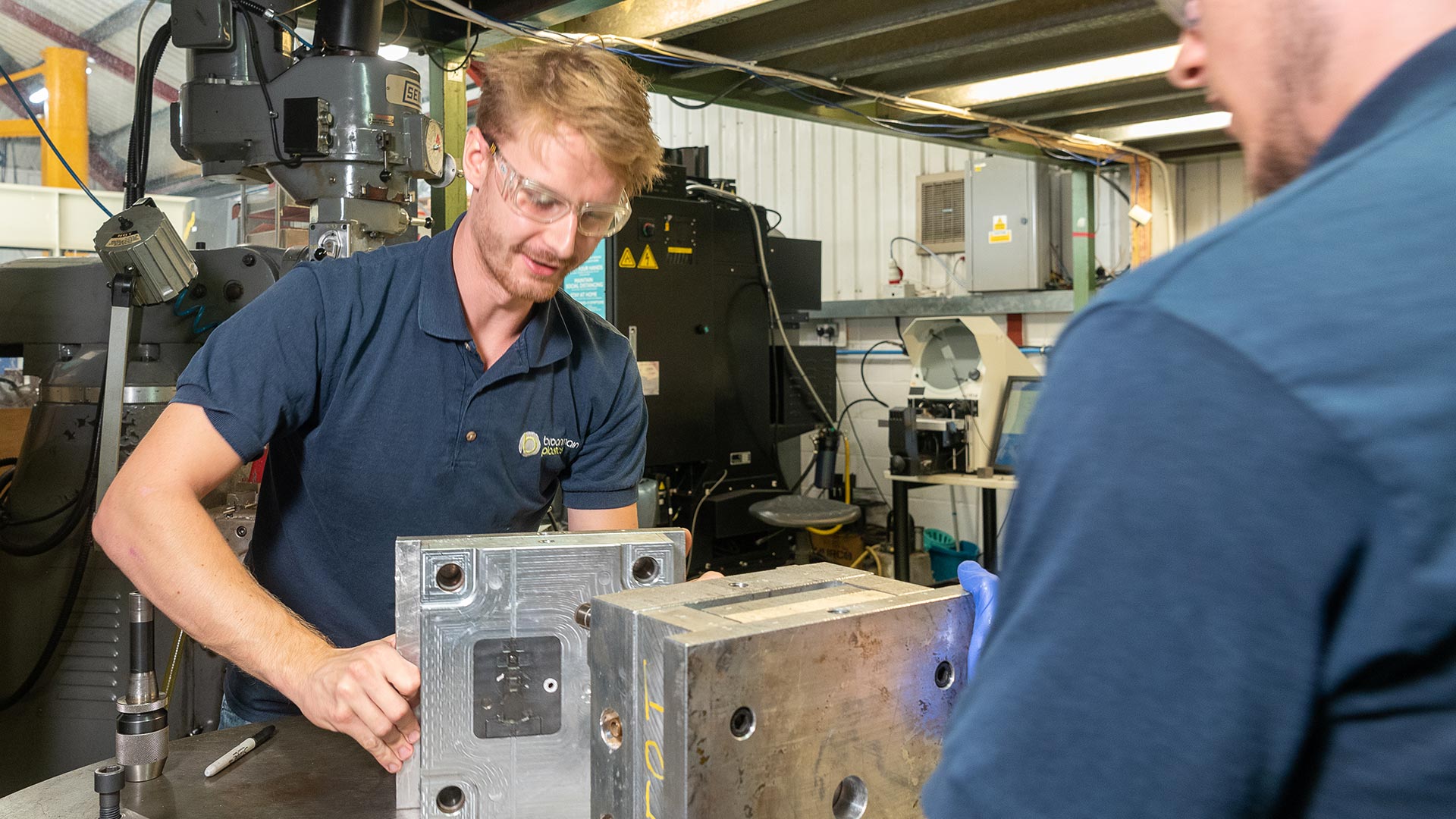
Broanmain Tool Shop Manager Kamil Stec shares the benefits of cross-departmental collaborations when working on mould tooling projects
Producing a perfect component starts with designing and building a perfect tool. Each project and part is as unique as the next. As a technical moulder with extensive toolmaking and processing experience, Broanmain Plastics shares how a cross-departmental collaborative approach to tool design can deliver enhanced functionality and moulding precision.
Engineering an injection moulding tool is a highly sought after skill, requiring the application of mathematics, science, material processing knowledge, creative problem solving and innovation.
In many respects, Broanmain was ahead of the Covid reshoring curve. Having invested in resourcing a modern tool room, customers, that might previously have relied on mould tools being sourced overseas, swiftly discovered the advantage of appointing a British firm to manufacture mould tools and customise inserts. Tool shop manager Kamil Stec cannot recall a busier time.
One of the most exciting tool designs over the last year, reflects Kamil, has been a new iteration of an existing product. It involved creating a complex 2+2+2+2 cavity family tool which is then used to mould polypropylene slider assemblies with an overmoulded TPE seal.
Quality in = quality out
While it is possible to design and manufacture a tool in isolation, there are so many factors to consider. What looks good on a blueprint might not deliver the quality and repeatability in a true production environment.
It’s always advisable to get a manufacturing production team involved in the prototype to consider what the final component will look like, the materials it will be made from and even the machines it will be made on. This helps to ensure that the final tool will deliver the desired result. Asking for an all-in fee, with a detailed breakdown and timeframe for mould tool development, testing and sign off, will help to avoid any hidden financial surprises.
The benefits of using a moulder with the in-house tooling expertise are threefold highlights Kamil. “When it comes to optimising the design, it is extremely useful to understand the moulding process and the nuances of the machine that the tool will be running on.” For this, Kamil collaborates with colleagues on the shop floor, Operations Manager Thomas Catinat, as well as Broanmain’s quality control and assembly professionals. He corroborates that having access to this all-round knowledge can be critical to a project’s success and meeting delivery timescales. “It’s beneficial for creating test samples, especially if you have to re-run tests before the tool is signed off,” adds Kamil.
Rather than shipping the tool and booking a slot with an external moulder, Kamil can run samples and get the approval parts in the same day. “It is so much faster as well as making it easier to modify and service the tooling and run samples again.” Kamil estimates that this to-and-fro process can equate to several lost production weeks.
From the clients’ perspective, having a single point of contact and no language barriers is equally advantageous. Kamil explains: “Sitting face to face with any customer and being able to show the tool and sample components means that we can usually deduce and correct any issues on-site within 24 hours.”
Master tool materials
There are two material choices to consider when it comes to the production of a tool: the tool material itself, plus the material for the final component. Selecting the right steel for the project requires an understanding of both aspects.
The choice will also be very dependent on the material being moulded, cycle-time expectations, the functionality of the component, production volumes, and maintenance. Although the price tag will clearly be an influential factor, the old adage that cheaper costs more eventually is an important consideration.
For wear resistance, a hardened steel like a nickel-chromium alloy (grade 2767), is ideal. The upfront tooling cost may be higher. However, long term it reduces maintenance costs. Conversely, hardened steels can be less thermally conductive, which can impact cooling time.
Similarly, the selection of material that’s injected into the mould tool is equally critical because different materials have different shrinkages. An ABS or polypropylene composite will react differently to a material containing glass fillers, for example. Other materials can be abrasive and will influence the wear and erosion of the mould tool.
Optimising TCTO
Making a bespoke tool does imply customisation to exact specifications. While this is true, a moulder will likely have a library of examples in their extensive tool room. Possibly similar components they’ve worked on. All of this background expertise can be leveraged to optimise Total Cost of Tool Ownership.
Although IP will restrict a moulder from ‘borrowing’ from a tool inventory, having proven technical capabilities means they won’t be rewriting the tool design rules from scratch. “This can be especially helpful if the design requirements at the outset are a little vague or ambiguous. It can also speed up the innovation cycle for tooling,” highlights Kamil.
Another strategy to help offset the cost of the tool development process is to examine an entire product portfolio and see if the same component could be used across a ‘family’ range.
“Being able to access the tool inserts and make changes to the master tool further down the line also helps to extend the longevity of a tool investment,” adds Kamil. “At Broanmain we store and maintain more than 1,000 tools to keep them in good working order. We also perform all repairs on site. With this type of attentive care, a well maintained tool should run at least half a million components. However, figures upwards of four million are not unusual.”
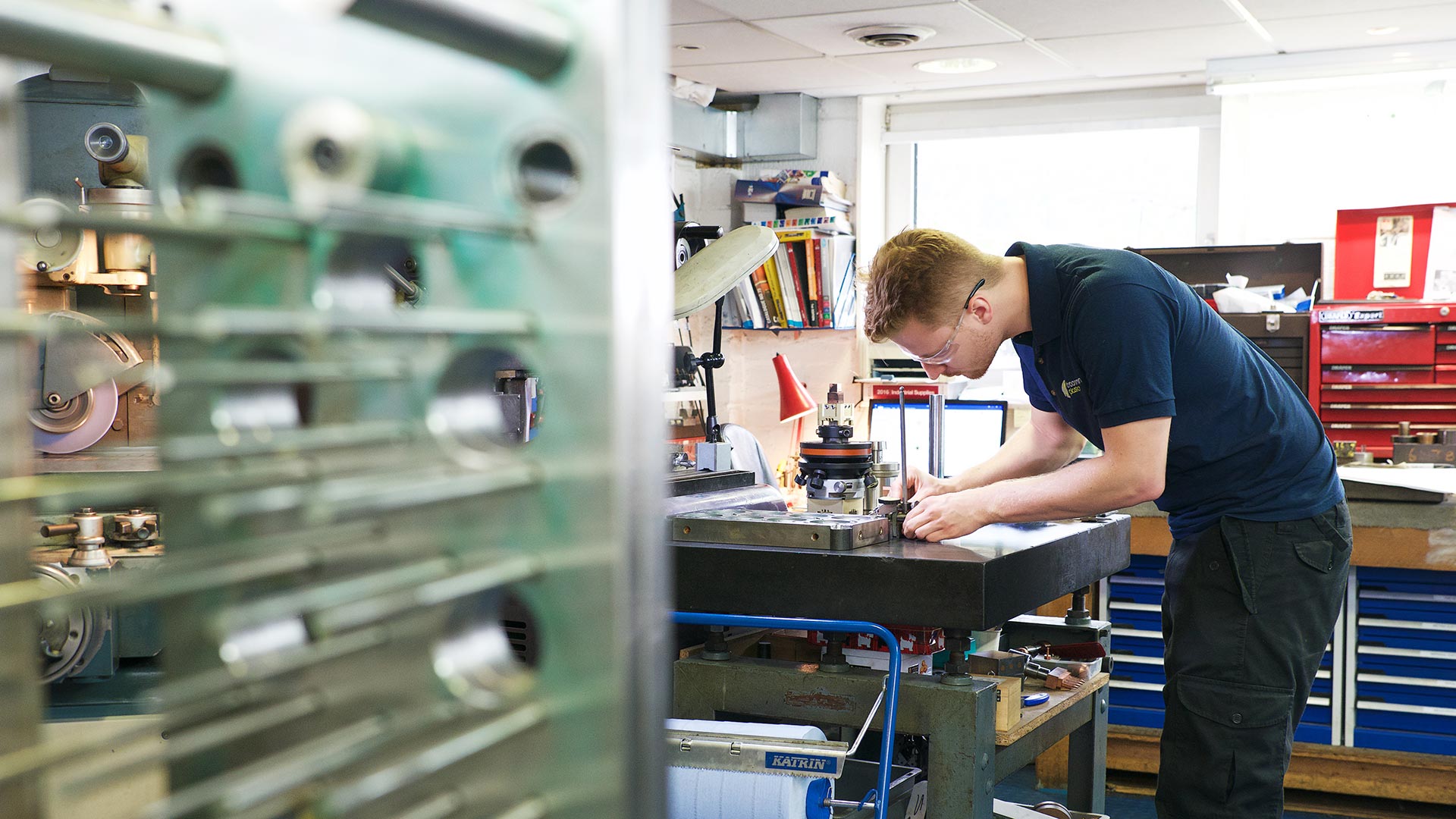
Broanmain Tool Shop Manager Kamil Stec shares the benefits of cross-departmental collaborations when working on mould tooling projects
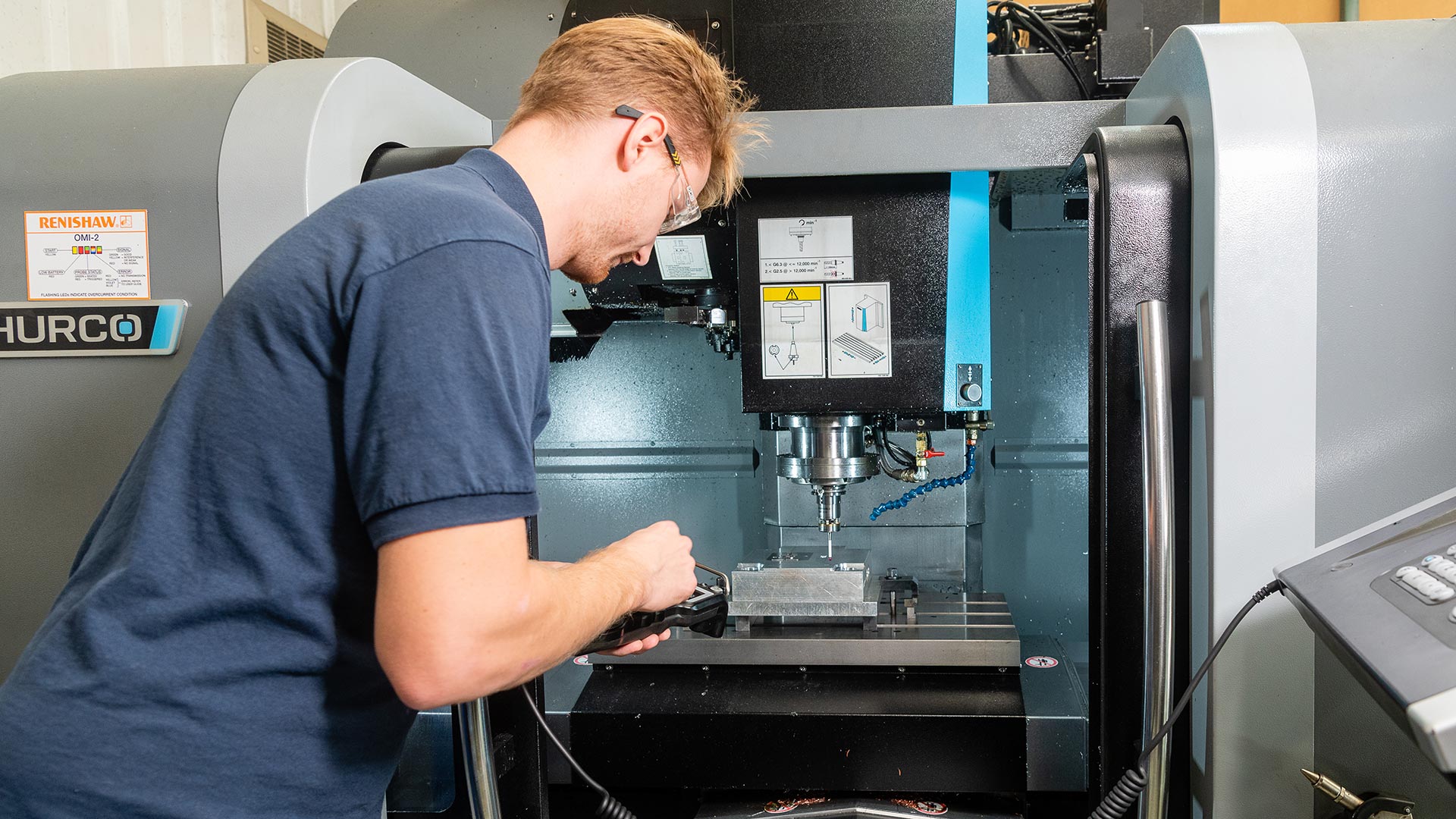
Broanmain Tool Shop Manager Kamil Stec shares the benefits of cross-departmental collaborations when working on mould tooling projects