Injection moulding is one of the most cost effective and precise ways to mass-produce plastic components. Some might say it’s a science. For Thomas Catinat, production manager at Broanmain Plastics, a good injection moulder combines art, chemical and applied engineering, all intersecting with technology.
A plastics processing engineering graduate from the Institut Superieur de Plasturgie d’Alencon (ISPA) in France – one of the few specialist institutes in the world – Thomas knows plenty about balancing usability and artistic aesthetics when advising on the design and overseeing the production of plastic components. There are numerous details to keep in mind. It’s not simply a case of pushing a button on a moulding machine and out pops a pipette or smart phone case. Injection moulding requires a deep understanding of structure, tooling, polymer chemical compositions, functionality and process, as well as finish and decoration.
With the global plastics moulding market forecast to reach US$690.bn by 2023[i], Thomas, shares just some of his polymer tips to assist customers innovate, curb costs, speed up time to market, select materials and achieve processing consistency.
Form and function
Pretty much any size, shape, strength and structure can be injection moulded, depending on budget and the size of the injection moulding machine. Ranging from plastic garden chairs, wheelie bins to microscopic components weighing less than 0.1g.
The thickness that can be moulded depends upon the grade of the raw plastic material. If the material doesn’t flow fast enough into the mould tool, or if the injection speed is too slow, there’s a high risk of the part freezing while the mould is still filling. This can cause a flow mark affecting the visual aesthetics, or worse a short shot resulting in a major product defect.
Cost also needs to be factored in. If the proposed plastic part is too thick, there might be a more financially viable material to use, for example a metal sheet.
Material choice
There are in excess of 85,000 listed plastic materials, and more than 45 polymer families. All offer varying degrees of strength, resistance, elasticity and even special features such as anti-bacterial or UV protection. The choice will depend on the application, for example if it needs to withstand high or extremely cold temperatures. For example, for one client Broanmain sources a WRAS accredited molymer for a water flushing device.
Narrowing the choices down can feel a daunting. Although most customers know what they want, an experienced moulder can make recommendations based upon the environment the component is being used in, and help customers to consider other usability factors, such as slide action.
Generally speaking, polypropylene (PP) is used when replacing metal components with plastic. It’s a relatively inexpensive resin, fairly robust, and commonly used in packaging applications, such as snap on lids or bottle caps, or medical tubing.
Acrylonitrile Butadiene Styrene (ABS) is also relatively inexpensive and typically used for most electronic housing, technology and consumer power tools. Standard ABS is usually mixed with the most appropriate additives to make them cleaner, safer, stronger and shinier. Common examples include colour pigments, anti static agents and heat stabilisers.
Mixing of the polymers in pellet or powder form is often performed by a material supplier, which a moulder buys in batches. However, most moulders, Broanmain included, have dosing units on site to create a polymer mix when smaller quantities are required.
Bioplastics
With such a focus on sustainability and reducing plastic consumption, customers invariably ask about the moulding properties of bio-based materials. Although the cost of bio-based materials is gradually coming down, the price currently remains higher than fossil-derived polymers. There still remain lots of developments in this field. And for many right now there are too many unknowns, including questions surrounding the true sustainability of harvested bio-based crops, such as corn.
For recycled plastics, the jury for many customers is also still out. Most prefer to source a pure polymer and don’t accept regrinds, as they are concerned that product performance will be compromised. From a scientific perspective, every time plastic is melted the molecular structure changes and degrades. Some call this a ‘heat history’. The more this happens, the more weak and brittle the part gets. In time this can affect the characteristics of the end product, potentially compromising safety, hygiene or performance.
If using regrind it’s advisable to minimise the blend to 20% or less. Do remember that any subsequent pass through the machines will contain some of the previous regrind blend, so the ratio of regrind to virgin polymer will increase incrementally.
Colour
Although the surface of plastics can be painted, pad printed or treated post moulding, using colour pigment additives ensures that the decorative features run through the entire product and won’t wear off. Pigments can also be used to create an opaque or refractive surface.
Streaking or colouring defects are often a result of the master batch material not being mixed properly. It could also be a result of contaminants or impurities being introduced via the hopper, material feed or mould plates. Often this is a result of poor cleaning and asset care.
Counterfeiting
In most instances, controlling the copying of a mass produced widget, cap or electrical connector is rarely worth the effort. However, for premium components, for example a high value watch casing, injection moulders can offer a number of counterfeiting measures to protect intellectual property.
Introducing a distinguishable feature, either by etching onto the component post moulding or through the insertion of an In Mould Label or barcode, is an easy way to combat counterfeiting. Other options could include introducing micro-dots or markers into the plastic resin before passes through the machine.
Process adjustments
Setting the moulding parameters, injection pressures and temperatures is a moulder’s sphere of expertise. Nevertheless, customers are often intrigued to understand how subtle tweaks can alter the look, feel and functionality of a component, as well as the production cycle time and waste.
Like most things in life, the process is not always perfect straight off. Best case scenario is 80% of the process parameters are solved when designing the part. These settings are then used as the benchmark to make small adjustments when the tooling and parts arrive at the mouldshop.
Adjusting the temperature of the barrel and stroke settings is typically the most complex, as just a minor modification affects the plastic viscosity. If there is texturing on the tool to create a shiny or matt surface, these adjustments could cause the plastic to stick to the tool surface.
Zero defects is the ultimate target. Creating a stable process is the goal. With so many variables, establishing the processing parameters is where an engineer’s skill is truly tested.
Validation
Quality Assurance is critical to all sectors, but medical and automotive especially. Performing a validation can be good business practice in all industries. Whether it’s mandatory however will depend on the part being manufactured and the sector it’s destined for.
Some moulders, Broanmain included, incorporate testing of parts in their quoted price. To avoid financial surprises always ask. Flexibility on the moulder’s part is vital, as some customers have more stringent Part Approval processes comprising the validation of tools and samples to ensure the design and processes are fit for purpose.
The QA process for medical devices is more convoluted, typically involving documenting the validation of the design, process set up and ongoing process stability for the full production lifecycle.
Other moulding techniques
Thermoset moulding is often regarded as a bit of a dying art. Broanmain is one of a handful of UK moulders that continues to offer this service. Performed on vertical machines, the plastic material is heated, compressed, cured and cooled in the mould itself, rather than injecting melted plastic into the tool. This technique is often used to produce legacy components or when high chemical or heat resistance is required.
Stack moulding is a relatively new and state of the art technique. Moulders use it to increase output. However, the tooling itself can be complex and costly to design, which is a deterrent for many.
Overmoulding involves adding an additional layer over an already moulded part. Where there are two parts to a component, for example a cable, overmoulding can help to eliminate assembly. It can also be used to add waterproofing and insulation.
Twinshot moulding is a variant of overmoulding and uses two different types of plastic, for example thermoplastics and liquid silicon, or two different colours. These are moulded at the same time, helping to reduce cycle times
Summing up, Thomas emphasises the importance of seeking a moulding partner that can think creatively and use their engineering acumen and scientific knowledge to present the best moulding options. “While today’s moulding machines are highly intuitive to operate, to achieve processing consistency requires large doses of creativity with an equal measure of scientific analysis and understanding of how the molecular structure of plastics change as they are processed,” ends Thomas.


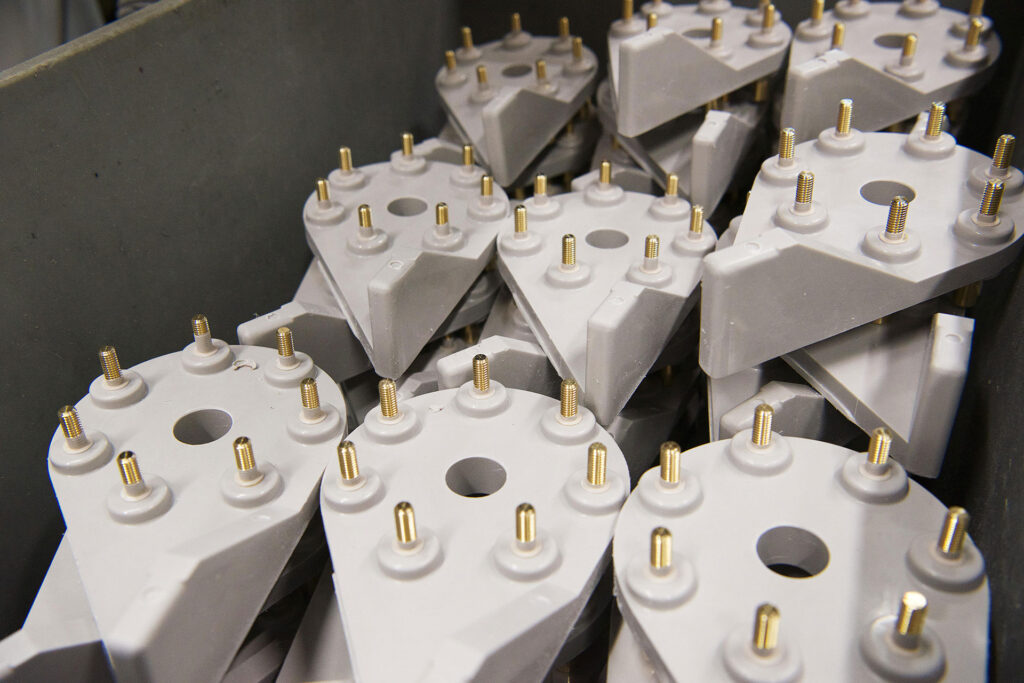