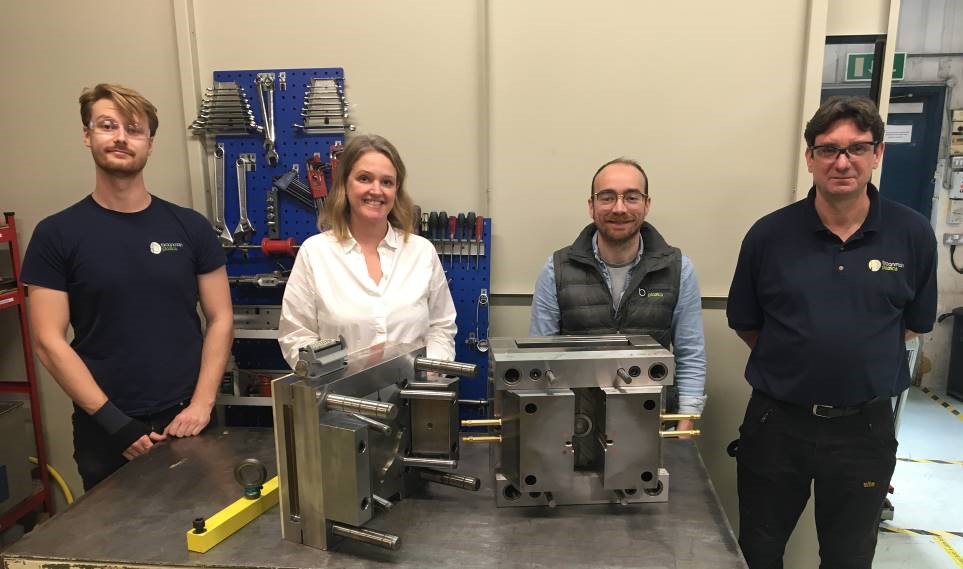
Tool room manager Kamil Stec (far left) headed the project from concept to delivery. Pictured with (from L to R) MD Jo Davis, operations manager Thomas Catinat and team member Andy Budd.
Using its newly equipped state-of-the-art tool room, the Broanmain Plastics team has developed a true cross-departmental collaborative approach to tool design and delivery.
Led by Kamil Stec and Thomas Catinat, the team now has capacity to complete tool design and delivery projects – engineering, crafting and testing – in house. The most recent project saw the completion of a single cavity slide action tool with a hot tip – which sees the company manufacturing the utility filter components in house for a leading UK OEM.
Kamil designed the drawings, sourcing over 200 individual tool components, and assembling the steel tool to the highest precision. Automating a previously time consuming and labour-intensive manual moulding process, the benefits of using a moulder with the in-house tooling expertise are threefold highlights Kamil. “When it comes to optimising the design, it is extremely useful to understand the moulding process and the nuances of the machine that the tool will be running on.”
In this instance, Kamil called upon the expertise of operations manager Thomas Catinat. With toolmaking being such an in-demand, highly skilled profession, having access to this all-round knowledge can be critical to the project’s success and moulding productivity and quality.
“It’s also beneficial for creating test samples, especially if you have to re-run tests before the tool is signed off,” adds Kamil. Rather than shipping the tool and booking a slot with an external moulder, Kamil ran samples and got the approval parts in the same day. “It is so much faster as well as making it easier to modify and service the tooling and run samples again.” Kamil estimates that this to-and-fro process can equate to several lost production weeks.
For the moulding samples, Dorking team member Andy Budd showcased his newly advanced testing skills. Having recently completed the Advanced Injection Moulding course at the Sumitomo (SHI) Demag Academy, Andy performed his first unsupervised tool trial with confidence and no glitches.
From the clients’ perspective, having a single point of contact and no language barriers is equally advantageous. Kamil explains: “Sitting face to face with any customer and being able to show the tool and sample components means that we can usually deduce and correct any issues on-site within 24 hours.”
To learn more call us on +44(0)1306 885888 or email info@broanmain.co.uk