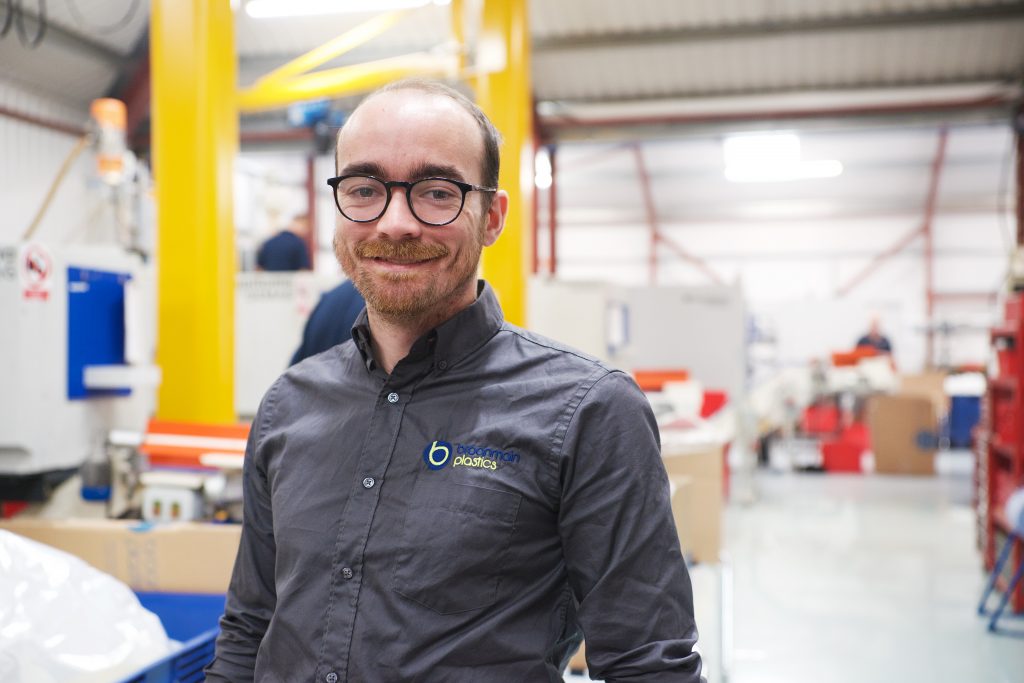
Thomas Catinat, operations manager at Broanmain Plastic
Injection moulding is one of the most cost effective and precise ways to mass-produce plastic components. A plastics processing engineering graduate from the Institut Superieur de Plasturgie d’Alencon (ISPA) in France, Broanmain’s operations manager Thomas Catinat discusses balancing usability with artistic aesthetics when making plastic components.
Injection moulding requires a deep understanding of structure, tooling, polymer chemical compositions, functionality and process, as well as finish and decoration.
Pretty much any size, shape, strength and structure can be injection moulded, depending on budget and the size of the injection moulding machine. Ranging from plastic garden chairs, wheelie bins to microscopic components weighing less than 0.1g. The thickness that can be moulded depends upon the grade of the raw plastic material.
Cost also needs to be factored in. If the proposed plastic part is too thick, there might be a more financially viable material to use, for example a metal sheet.
Material choices
There are in excess of 85,000 listed plastic materials, and more than 45 polymer families. All offer varying degrees of strength, resistance, elasticity and even special features such as anti-bacterial or UV protection. The choice will depend on the application, for example if it needs to withstand high or extremely cold temperatures.
Experienced moulders can make recommendations based upon the environment the component is being used in, and help customers to consider other usability factors, such as slide action.
Typically, polypropylene (PP) is used when replacing metal components with plastic. It’s a relatively inexpensive resin, fairly robust, and commonly used in packaging applications, such as snap on lids or bottle caps, or medical tubing.
Acrylonitrile Butadiene Styrene (ABS) is also relatively inexpensive and often used for most electronic housing, technology and consumer power tools. Standard ABS is usually mixed with the most appropriate additives to make them cleaner, safer, stronger and shinier. Common examples include colour pigments, anti static agents and heat stabilisers.
Bioplastics
Although the cost of bio-based materials is gradually coming down, the price currently remains higher than fossil-derived polymers. There still lots of developments in this field and too many unknowns, including questions surrounding the true sustainability of harvested bio-based crops, such as corn.
Most customers prefer to source a pure polymer, as they are concerned that product performance will be compromised using recycled regrinds. From a scientific perspective, every time plastic is melted the molecular structure changes and degrades. Some call this a ‘heat history’. The more this happens, the more weak and brittle the part gets. In time this can affect the characteristics of the end product, potentially compromising safety, hygiene or performance.
If using regrind it’s advisable to minimise the blend to 20% or less.
Colour
Although the surface of plastics can be painted, pad printed or treated post moulding, using colour pigment additives ensures that the decorative features run through the entire product and won’t wear off. Pigments can also be used to create an opaque or refractive surface.
Streaking or colouring defects are often a result of the master batch material not being mixed properly. It could also be a result of contaminants or impurities being introduced via the hopper, material feed or mould plates.
Process adjustments
Setting the moulding parameters, injection pressures and temperatures our sphere of expertise. Nevertheless, customers are often intrigued to understand how subtle tweaks can alter the look, feel and functionality of a component, as well as the production cycle time and waste.
Like most things in life, the process is not always perfect straight off. Best case scenario is 80% of the process parameters are solved when designing the part. These settings are then used as the benchmark to make small adjustments when the tooling and parts arrive at the mouldshop.
Adjusting the temperature of the barrel and stroke settings is typically the most complex, as just a minor modification affects the plastic viscosity. If there is texturing on the tool to create a shiny or matt surface, these adjustments could cause the plastic to stick to the tool surface.
Zero defects is the ultimate target.
Validation
Quality Assurance is critical to all sectors, but medical and automotive especially. Even if not mandatory, performing a validation can be good business practice for all industries.
Some moulders, Broanmain included, incorporate testing of parts in the quoted price. To avoid financial surprises always ask. Some customers have more stringent Part Approval processes comprising the validation of tools and samples to ensure the design and processes are fit for purpose.
Summing up, Thomas emphasises the importance of seeking a moulding partner that can think creatively and use their engineering acumen and scientific knowledge to present the best moulding options.
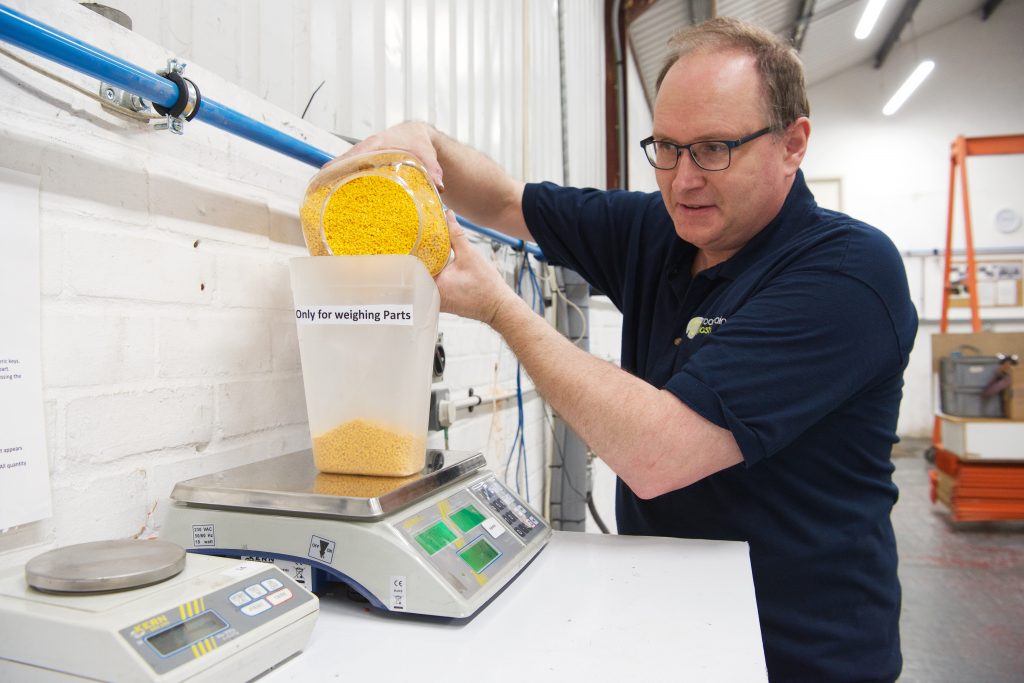
Polymers offer varying degrees of strength, resistance, elasticity and even special features such as anti-bacterial or UV protection